
Crawfordsburn Passive House Construction Diary 2013
This Passivhaus design achieves the ‘Fabric first’ ultra-low energy German Passivhaus Institute Standard. The main living spaces, such as the kitchen and double-height living room have been designed to the south elevation to maximise heat gain from the southern sun. The balcony feature from the master bedroom acts, not only as a feature balcony but as a design tool to provide appropriate shading in the summer to prevent overheating. This modern Passivhaus is situated on a cluster of farmyard buildings and its simple design is integrated into the surrounding context.
The rigorous Passivhaus design approach must be woven into a design from the beginning. This makes the building environmentally responsible and uses the following criteria as design benchmarks.
Super-insulated walls, floor and roof
Use of Mechanical Heat Recovery System and ventilation
Passivhaus approved triple glazing and external doors
Use of Thermal Bridge analysis to reduce heat loss at junctions
South-facing glazing to maximise Passive Solar heat gains in winter
Passivhaus design has many advantages over conventional construction and design techniques, it offers a modern and comfortable dwelling with no cold drafts, no temperature variations from room to room, a quiet internal environment and significantly reduced running costs. The house Crawfordsburn Passive House has now been lived in since 2013 and has hosted several Passive House open days. The feedback from the owners on both energy efficiency and comfort has been very positive.
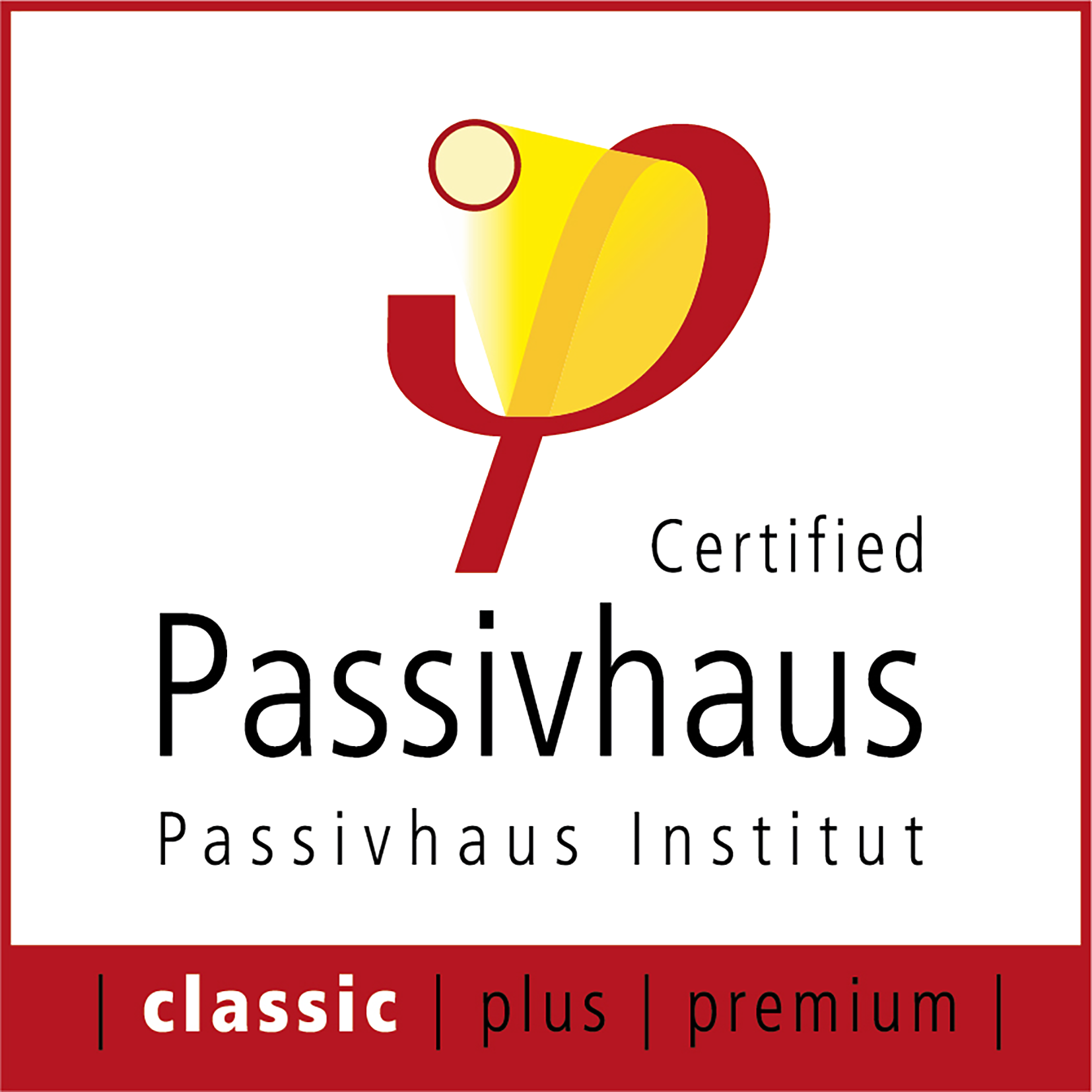
Follow the story of this construction project with 24 diary entries
Today the Crawfordsburn passive house certification became official as we received the documentation from MosArt! The dwelling is now a certified Passivhaus building
We, at Paul McAlister Architects are revealing the costs of the Crawfordsburn passive house. The dwelling is to have a total area of 220.6sqm/2375sqft. The following offers a breakdown of the construction costs, including site works, building envelope and fixtures and fittings.
The Crawfordsburn passive house is in the final phase of works, the internal plastering and external rendering are now complete. The bathrooms and kitchen are being installed, as are internal doors and the glazed internal balcony.
The applied Passivhaus approach dramatically reduces the demand for space heating which means the house does not require a conventional central heating system. The space heating demand will be 14kWh/(m2/a) for the entire house.
The ventilation system, with heat recovery, is an integral component of the dwelling, essential for achieving the Passivhaus certification performance levels. A proven low-energy and highly efficient ventilation method, MVHR is fast becoming the most common method of whole home ventilation for new build properties
The airtightness, as already mentioned in previous diary entries, is crucial for the overall success of the passive house. We have discussed the high risk air leakage components such as wall openings, floor-to-wall junctions and wall-to-roof junctions.
The build has continued to proceed well; it is very exciting seeing each step of construction completed. The snow arrived on site recently making the working conditions rather cold for the construction team! Many sub-contractors are starting to appear on site to play their part in various installations
Steady progress was made on site this week as we saw the internal membranes on the walls being fitted. The build is really coming together.
All windows and doors utilised in Passivhaus certified buildings have to meet certain performance criteria. The wall openings have been discussed in the previous diary entry but here we will detail the exact capabilities of the window and doors units.
After a slight delay, this week saw the installation of the windows and doors in the Crawfordsburn passive house. We have decided to use this diary entry to address how we’ve dealt with the window and door openings. In the next entry we will discuss the specific window and door units.
In the last diary entry we announced that the timber frame construction kit had arrived on site. In the past two weeks it has transformed from individuals panels into an actual dwelling. It has been fantastic to witness and we feel like the build is really starting to take shape now.
So the big day is here, the timber frame kit has finally arrived! We will have lots of photos documenting the frame as it is erected over the next few weeks, so keep your eyes peeled. For now the photograph below shows the frame unloaded on to the site ready for construction to commence tomorrow.
We spoke too soon when we boasted about everything running on time! This week marked the start of the waiting game ... SIPFIT our timber frame manufacturer is running slightly behind schedule so were anxiously awaiting the arrival of the SIP Panels which should be any day now, fingers crossed.
In order for the building to perform as efficiently as possible, material choice throughout has been extremely important. As we progress through the dwelling build we will discuss in depth each of the materials we are using and the reasons why.
The product utilised for this construction is Foamglas® Perinsul. Foamglas® Perinsul is a very high density speciality product used to eliminate structural thermal bridging. All sides are bitumen coated. The upper and the lower surface of the insulation are additionally coated with glass reinforced fleece.
As previously discussed we had identified two independent timber companies that could supply the timber construction kit for the Crawfordsburn passive house. As the two systems have slight differences we have had to alter some of our drawings to suit the selected panels.
This week saw Baylands Construction Ltd place the footings and start work on the dwellings’ blockwork substructure. Kevin and the team have had relatively good weather to date which has eased the working process.
After an intensive year of research, design and planning the Crawfordsburn passive house is now ready for construction to commence. The design process, extensive Passivhaus calculations, planning application, building control application and contract tender process are now all complete.
Almost three weeks have passed since our last diary entry, during which time we have been very busy collecting construction tender returns and selecting the contractor for the Crawfordsburn passive house.
Now that we have our tender package ready to go the challenge is not pricing the construction works but rather getting contractors who have the skill and knowledge to actually build it.
Just over two weeks have passed now since our last diary entry. Since then we have been in continual correspondence with Mosart regarding our submission and we are now pleased to report that they will assure that the building will perform as a Quality Approved Passive House provided that the following criteria is met.
The Crawfordsburn passive house is almost ready for construction to commence. The design process, planning application and building control application are now all complete. The next stage in the design process is the completion of the PHPP (Passivhaus Planning Package) file and the Design Stage Assurance.
Over the following months, Paul McAlister Architects will be posting a regular diary documenting the construction of the much anticipated Crawfordsburn Passive House in Co. Down, Northern Ireland.
Here is a list of the team involved in the design and construction of the Crawfordsburn passive house